Lifting and Rotating Large Plastic Rolls With Ease
About The Company
Established in 1882 in Brownsburg, IN, Weston Foods boasts a rich legacy as a pioneer in the milling industry, specializing in rice and gluten-free flours. The company was founded by a group of highly skilled individuals with extensive experience in crafting top-notch gluten-free ingredients. Guided by principles of service, quality, and value, Weston Foods has flourished over the years to emerge as one of the foremost millers of gluten-free ingredients. Positioned as a leader in allergen-free food security, the company has consistently prioritized delivering excellence to its customers.
The company operates 16 facilities spread across 13 states, producing a diverse range of fresh and frozen baked goods. From doughnuts, cakes, and pies to cupcakes, cookies, crackers, cones, ice cream novelty products, and artisan bread, Weston Foods’ extensive product line graces the shelves of North American grocery retailers, supermarket chains, and various food service outlets.
Weston Foods commitment to quality extends beyond mere products; it’s a dedication to providing allergen-free food solutions that meet the highest standards. With a focus on freshness, innovation, and customer satisfaction, they continue to lead the way in delivering delicious, safe, and top-quality baked goods to households and businesses across North America.
Load Specifications
- Load Type: Plastic Rolls
- Weight: 145 lbs
- Size: Diameter – 18” Width- 22” ID- 3”
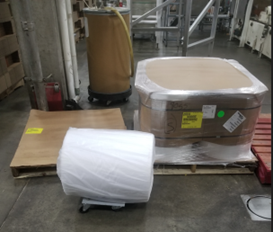
Application Analysis
Lifting plastic roll weighing 145-lb from a pallet while roll is standing vertical. Once the roll is lifted it needs to be rotated 90-degrees and placed on a dolly for transport to the production area.
Key Points:
- Pick up point- from a pallet, roll in vertical orientation standing 48” high
- Rotate – 90°
- Place point- horizontal onto a dolly at 5”
- Area of coverage- 6-8’
- Cycle time- 5/hr.
Handling Issues
The handling procedure was being completed by hand manually which was causing safety issues. Additionally, heavier rolls would require 2 workers to accomplish the task, decreasing productivity.
The Solution
When considering the load weight and cycle time, ASE specified an ERH-200 portable, semi-powered floor-based Roll handler. The unit is designed to be manually pushed and included powered lift & manual turn functions. This light-weight unit is easy to move and grips the roll by the core, by way of an expanding mandrel with fail-safe spring force grippers. Once the expanding mandrel is inserted into the roll, the operator is then able to lift and turn it °90 so the roll can be placed eye to the horizon onto a portable dolly (designed for roll handling) which we also specified for the size and weight of their rolls. We included a handle bar and floor locks for functionality & safety. Weston Foods was able to eliminate the use of multiple workers by implementing the ERH-200 roll handling device which allowed them to achieve their goals and add ergonomics and safety to their roll handling process.
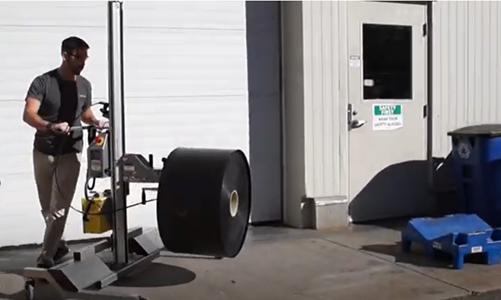
Key Technologies
- ERH-200 portable, semi-powered floor-based Roll handler
Some of the standard features on the ERH-200 include:
• Quiet 2-Speed Drive
• Lightweight Construction
• Micro-movement Control
• Quick-Change Battery Box
• Quick-Change Tooling Mount
• Battery-Charge Meter
• Manual Grip Tooling.